Just enter the given values for trace thickness, substrate heights, trace width and substrate dielectric in the calculator above and press the 'calculate' button. The default units for all given values, except the substrate dielectric, is in mil. It is possible to select other units. Trace Width Calculator FAQs Q: Is there a limit to the amount of current this tool can calculate a width for? The IPC-2221 data from which these formulas are derived only covers up to 35 Amps, trace width up to 400 mils, allowable temperature rise from 10 to 100 degrees Celsius, and copper of 0.5 to 3 ounces per square foot. The trace impedance on your PCB that carries RF signals can also be made 50 ohms by adjusting its width appropriately. You can calculate the trace width using online trace impedance calculators or microstrip impedance calculators. It is also easy to find parts (such as filters, amplifiers, antennas, etc) with 50 ohms characteristic input/output.
Keep your board cool with our PCB trace width vs. current table
Additionals MATSHITA DVD-RAM UJ8A2AS resources (included MATSUSHITA - MATSHITA PANASONIC drivers) MATSHITA UJ8A2AS CD DVD HD-DVD BLU-RAY Writer Firmware 1.40 was presented for free download to install, update, manage MATSUSHITA - MATSHITA PANASONIC CD DVD HDDVD BLURAY. MATSHITA DVD-RAM UJ8A2AS Drivers Download In our share libs contains the list of MATSHITA DVD-RAM UJ8A2AS drivers all versions and available for download. To download the proper driver by the version or Device ID. If not found in our garage driver you need, please contact us, we will help you in time, and updates to our website. Matsushita dvd ram uj8a2as driver download 64-bit.
Copper is a strong conductor with high melting point, but you should still do your best to keep temperatures low. This is where you’ll need to properly size trace widths to keep temperature within a certain limit. However, this is where you need to consider the current flowing in a given trace. When working with a power rail, high-voltage components and other portions of your board that are sensitive to heat, you can determine the trace width you need to use in your layout with a PCB trace width vs. current table.
One problem with most tables is that they are not built to account for controlled impedance routing. One you’ve sized your traces for controlled impedance, it can be difficult to determine the temperature rise just by looking at a table, and you’ll have to work with a calculator. However, one alternative is to use the IPC 2152 nomograph to check that the current-temperature relationship will be within your operating limits in controlled impedance traces. We’ve compiled this information here for your convenience.
Keep Temperature Low in High Voltage/High Current Design
During my day job, I find myself spending quite a bit of time browsing EE forums. One question that often comes up in the context of PCB design and routing is determining the recommended trace width required to keep your device’s temperature within a certain limit for a given current value, or vice versa. While copper has a high melting point and can withstand a high temperatures, you should ideally keep the temperature rise in your board within 10 °C. Allowing your PCB traces to reach very high temperatures increases the ambient temperature seen by components, which puts greater load on active cooling measures.
The IPC 2152 standards are the place to start when sizing traces and vias. The formulas specified in these standards are straightforward for calculating current limits for a given temperature rise, although they do not consider controlled impedance routing. That being said, working with a PCB trace width vs. current table is a great way to start when determining your PCB trace width/cross sectional area. This allows you to effectively determine an upper limit on the allowed current in your traces, which you can then use to size your traces for controlled impedance routing.
When the temperature rise reaches a very large value in a board running at high current, the electrical properties of the substrate can exhibit a corresponding change at high temperature. The electrical and mechanical properties of your substrate will change with temperature, and the board will become discolored and weak if run at high temperature for a long period of time. This is one reason the designers I know will size traces such that the temperature rise is kept within 10 °C. Skyrim character creation formulas. Another reason to do this is to accommodate a broad range of ambient temperatures, rather than considering a specific operating temperature.
The PCB trace width vs. current table below shows a number of trace widths and corresponding current values that will limit your temperature rise to 10 °C with 1 oz/sq. ft. copper weight. This should give you an idea of how to size traces in your PCB.
Different trace thicknesses/copper weights. The trace thickness needs to be calculated from the copper weight in your board. We’ve only included the standard 1 oz/sq. ft. value above. However, boards that will run at high current often require heavier copper to accommodate a higher temperature rise.
No impedance data. If you need to use controlled impedance routing, then you need to verify that your calculated trace dimensions will satisfy the limits specified above.
Alternative substrates. The above data is compiled for FR4, which will cover a broad range of PCBs sent to production. However, advanced applications may require an aluminum core PCB, ceramic substrate, or advanced high-speed laminate. If you work with a substrate with higher thermal conductivity, then the temperature of your traces will be lower, as more heat is transported away from warm traces. To a first order approximation, the temperature rise will be scaled by the ratio of the thermal conductivities of your desired substrate material to that of FR4.
Using the IPC 2152 Nomograph
If you want to work with different copper weights, verify controlled impedance routing dimensions against temperature rise and current, then you should use the nomograph from the IPC 2152 standards. This is a great way to size conductors for a specific current and temperature rise. Alternatively, you can determine the current that will produce a specific temperature rise if you have already chosen your trace width.
This is shown in two examples in the nomograph below. Note that the top half of the graph shown below is defined for internal traces only. To see the same version of this graph for external traces, see this article by Jeff Loyer.
IPC 2152 nomograph for PCB trace width vs. current and temperature rise. Image modified from user Daniel Grillo on StackExchange.

The red arrow shows how to determine the maximum current for a desired trace width, copper weight (i.e., trace cross section area), and temperature rise. In this example, the conductor width (140 mils) is chosen first, and the red arrow is traced horizontally over to the desired copper weight (1 oz/sq. ft.). We then trace vertically to the desired temperature rise (10 °C), and then we trace back to the y-axis to find the corresponding current limit (~2.75 A).
The orange arrow goes in the other direction. We’ve started with a desired current (1 A) and traced horizontally to our desired temperature rise (30 °C). We then trace downwards vertically to determine the trace dimensions. In this example, suppose we specify a 0.5 oz/sq. ft. copper weight. After tracing down to this line, we trace horizontally back to the y-axis to find the conductor width of ~40 mils. Suppose we wanted to use a copper weight of 1 oz/sq. ft.; in this case, we would find that the required trace width is 20 mils.
Verifying Controlled Impedance Routing
Let’s look at a simple example involving the above nomograph for use with a 50 Ohm microstrip trace on top of 4.7 mil laminate. If you use a microstrip trace impedance calculator, you’ll find that a trace thickness of 2 mils requires a trace width of 6.5 mils. We can now use these values in the above nomograph to determine the current limit for a given temperature rise (see the example for the red line). If we specify a maximum temperature rise of 10 °C, we see that the maximum current allowed in this trace is ~400 mA.
The powerful PCB layout and routing tools in Altium Designer® are built on a single unified design model that allows you to specify the trace and via sizes you need within your design rules. Altium Designer also includes a powerful stackup manager with a field solver for determining controlled impedance in your board. As you design your board and route your traces, the DRC engine will automatically check your design rules while ensuring your traces are properly sized to keep your temperature within the required range. This is much easier than manually routing traces and checking dimensions against a PCB trace width vs. current table.
Now you can download a free trial of Altium Designer and learn more about the industry’s best layout, simulation, and production planning tools. Talk to an Altium expert today to learn more.
ANSI PCB Trace Width Calculator
Help us improve these pages - If you have any comments about the content here or would like to see improvements or a different calculator added, please use the guest book.
New features in this version include:
- use of metric or imperial units for all major fields
- the ability to change units for any applicable field on the fly
- minor enhancements to some of the calculations - IPC-2221(A) changes the curve fit
- saving of all parameters in a cookie to keep your preferences between visits
ANSI PCB Trace Width Calculator | |||||||
---|---|---|---|---|---|---|---|
Input Data | Results Data | ||||||
Internal Traces | External Traces | ||||||
Field | Value | Units | Trace Data | Value | Units | Value | Units |
Current (max. 35A) | Required Trace Width | ||||||
Temperature Rise (max. 100°C) | Cross-section Area | ||||||
Cu thickness | Resistance | Ω Ohms | Ω Ohms | ||||
Ambient Temperature | Voltage Drop | Volts | Volts | ||||
Conductor Length | Loss | Watts | Watts | ||||
Peak Voltage | Volts | Required Track Clearance |
This page calculates approximations to the ANSI / IPC-2221/IPC-2221A design standards for PCB trace width - this is the replacement for IPC-D-275.
The approximations and rationale are described in Trace Currents and Temperatures Revisited by Douglas Brooks, UltraCAD Design, Inc.
The figures returned by this calculator are to be taken as a guide only. I will not be held responsible for any mishap or loss, either direct or consequential, that may occur as a result of relying on the figures herein.
The trace width formulas are:
External traces: I = 0.048 x dT0.44 x A0.725
where:
dT = temperature rise above ambient in °C
A = cross-sectional area in mils²
Please note that IPC-2221(A) equations are subtly different from those in IPC-D-275 in that they are typically slightly more conservative and are impicitly derated to compensate for manufacturing effects, i.e. they should be more reliable in practice.
The values calculated here compare very closely with those derived by the UltraCAD PCBTEMP utility, and like the diagrams in the standards documents, are valid up to 35A for external traces and 17.5A for internal, 400mil widths and a maximum temperature rise of 100°C.
I've added a recommended track clearance value based on the UL rule:
The formulae as it stands is simplistic, but is reasonable for V > 50. Note that there are many international standard for this sort of thing, e.g. EN60065:1994, which for European mains of 230V, allows for about 120mil for Class I (protected by earthing) and 240mil for Class II (double isolated). Note that if there is no conformal coating and the environment is dirty/humid/condensing then all bets are off. Please read the standards documents yourself.
Ideally, keep 'hot' and 'cold' areas of your board well apart.
Change a value in an input field, then press TAB to move to the next field. The results tables will be updated automatically.
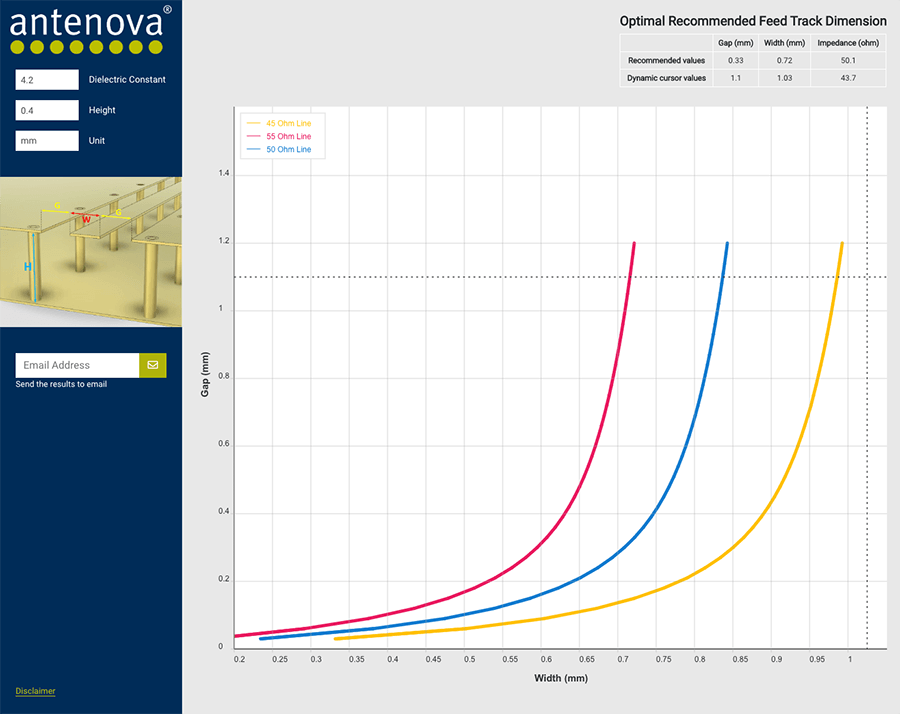
50 Ohm Trace Width Calculator
Back50 Ohm Transmission Line Calculator
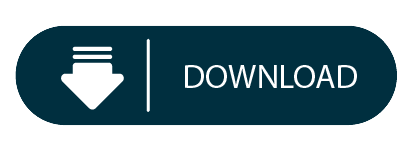